“Everyone wakes up to the sound of adhan, and we to the sound of the anvil”
The Story of Master Blacksmith Namig
Gunel Isayeva
For 35 years, artisan Namig has been forging iron on an anvil, heating steel in a furnace, and grinding it on a stone wheel. A small forge, conveying the atmosphere of past centuries, is his second home. From dawn to dusk he is there. He has many orders, he works hard, and the work he does is that of a master.
Namig Rzayev, 52, is the grandson of Dovlat, a well-known blacksmith in Goychay, and the son of craftsman Mokhlat. He learned this craft from his father and grandfather.
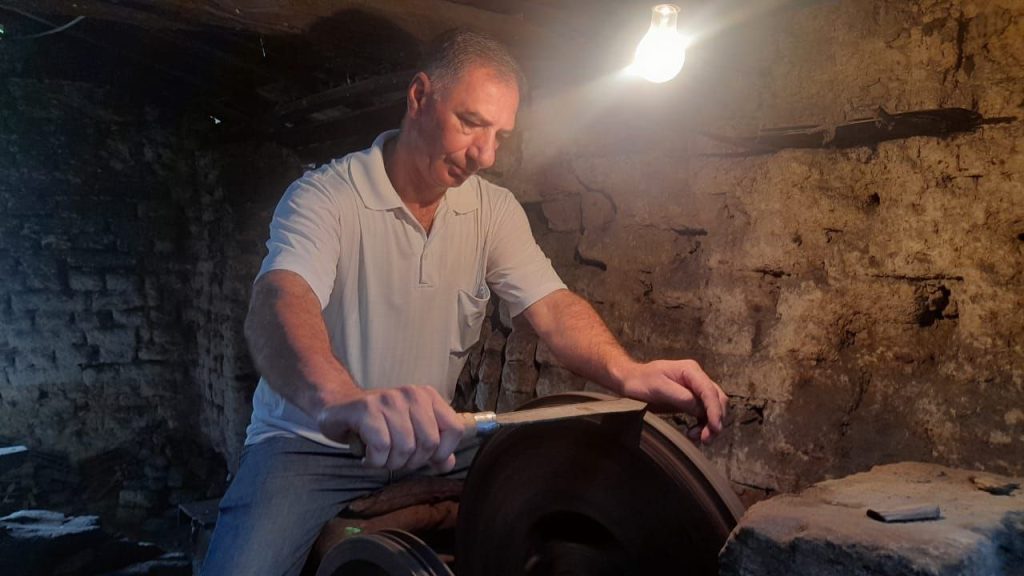
- 12 days in a Baku rehabilitation center
- “If your protesting hand gets tired, I’ll be there to take it”
- Viticulture in Azerbaijan developing in the shadow of officials
“I worked hard until I learned the trade”
“My great-grandfathers moved from Dagestan to Goychay in 1915. We are Lezgins by nationality. Since moving here they were engaged in blacksmithing and tinning. My grandfather made a name in blacksmithing. I try to keep his craft and name alive. Two of my uncles and my father were also engaged in this trade.
At first I was not interested in it, because I was into sports. And later I felt drawn to the craft. I watched and watched, sitting next to my father and trying to learn. I worked hard until I learned this business. I even broke tools, but I did not give up and eventually learned. You have to strike while the iron is hot to take shape. So it is with learning a trade.
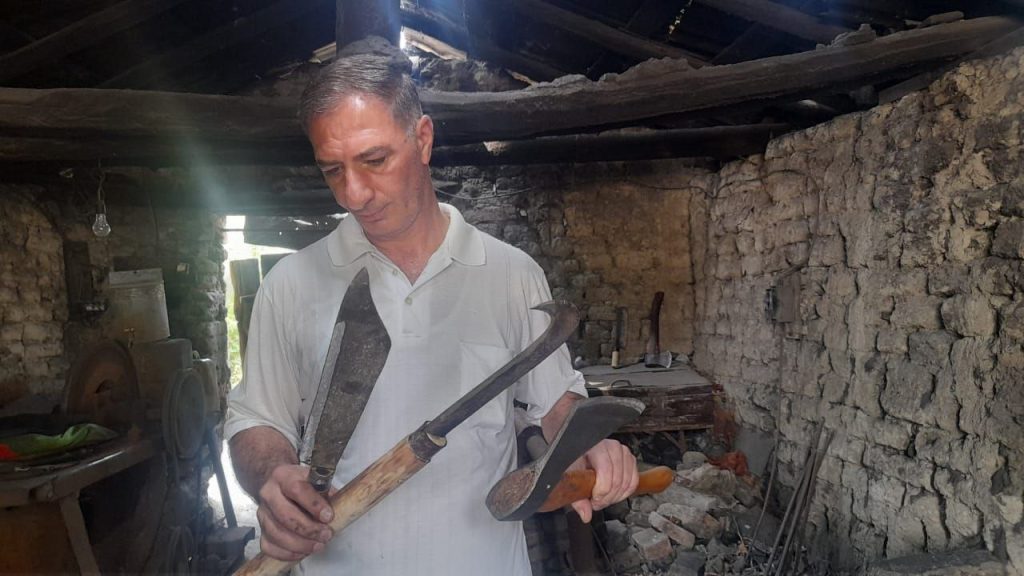
I get up at 6 am and start working. My workshop is open until 20:00. Whatever the order, I process and deliver it in such a way that the customers do not remain dissatisfied with me and that the work is ready for the arrival of the clients. There is no exact work schedule. From September to March there is work for every day. Then orders decrease. I work three, five hours a day. I repair and grind agricultural and household equipment, including knives, axes, teeth of electric machines. Everyone wakes up to the sound of adhan, we wake up to the sound of the anvil.”
“We miss the atmosphere of the artisans of the past”
The forge is over a century old. It has been recognized as a historical monument by the Ministry of Culture and Tourism. It is located on the central avenue of the district center, on the side of the road. It has a strange look. Although the sunlight seeping through the mudbrick walls and the old roof makes it difficult for the craftsman to work in the summer, it creates a pleasant atmosphere at other times of the year.
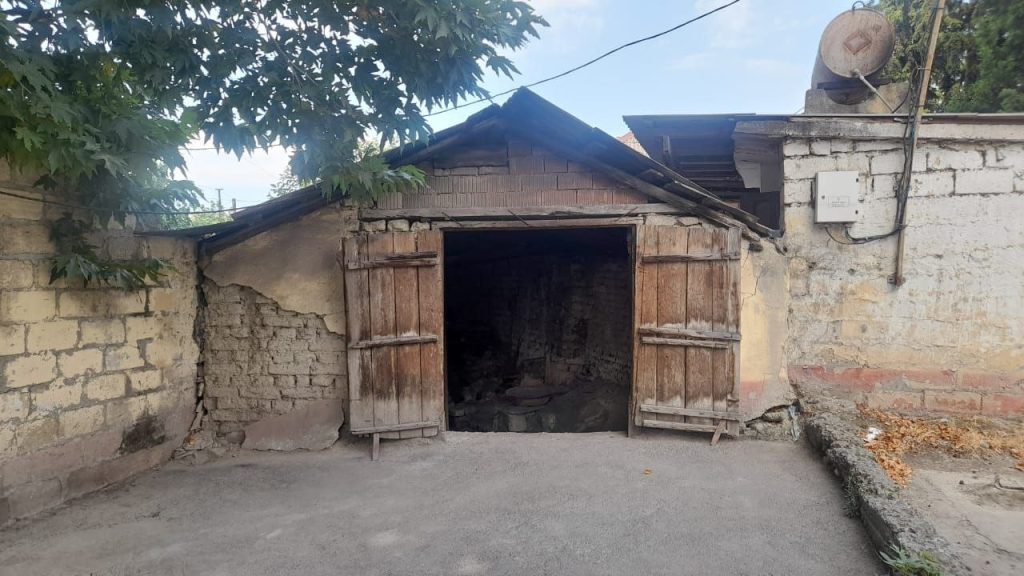
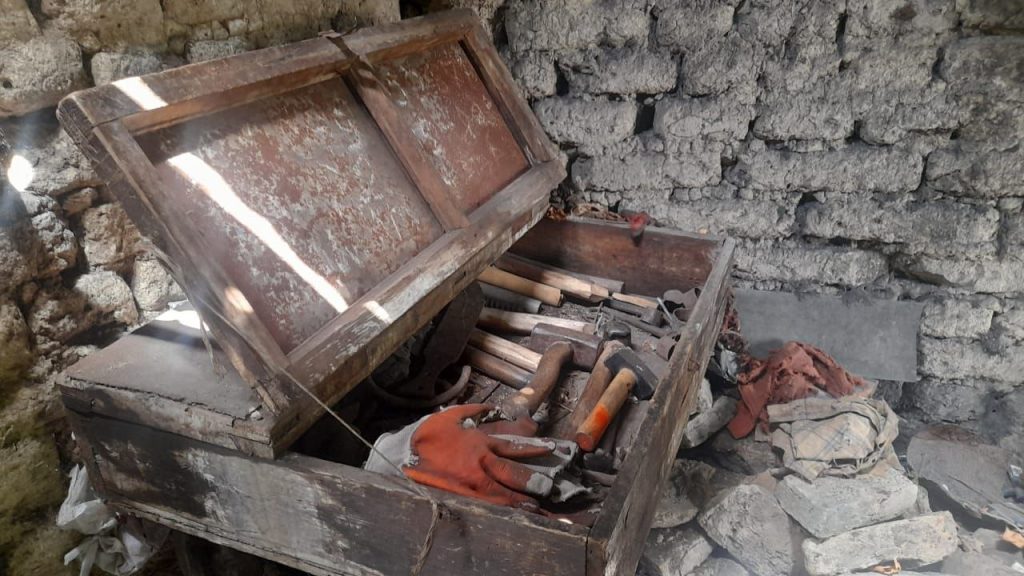
The equipment in the workshop is as old as the forge itself. A stone anvil, ancient hammers, tongs, a stone blower, a hearth, a stone wheel, a tool chest in the corner, and a steel crowbar hanging on the wall.
Goychay is known as the “Lezgi quarter”. In the past, the area was also known as the area of blacksmiths and tinkers.
Namig says that at this moment there are 15 Lezgin families left in their quarter. There are about 400 such families in the entire region. In the 90s of the last century, harsh living conditions, accompanied by the first Karabakh war, forced Russian, Armenian and Jewish families living in the region to sell their homes and move. During that period, the number of Lezgins also decreased, but many of them still remained in their native land. And those who remain are concerned that the historic craft center in Goychay is not getting the attention it deserves, and instead artisans are left with nothing to do and their space.
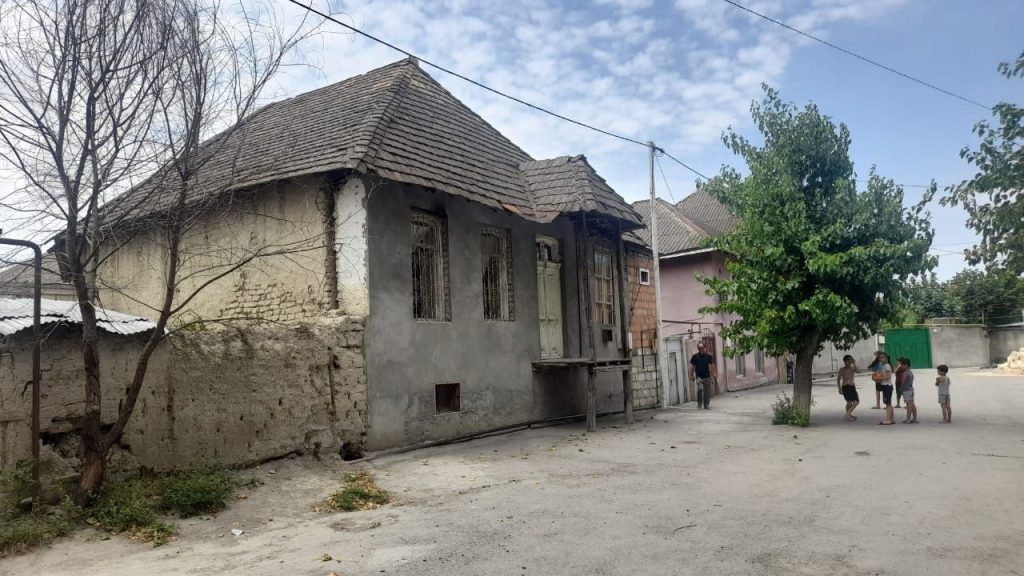
“There is a children’s entertainment center, about ten tinsmiths and blacksmiths worked around it. Then they sold their workshops and houses to the rich, and the artisans lost their space. Many old masters have passed away, and among their children there are those who continue this work in their yards, and those who are not. But those who are engaged in this business, gradually also leave it. Because there is no demand, no one appreciates.
This quarter could be preserved as a historical museum, at the entrance to which one could see different crafts. But almost the entire block has been sold. Artisans have to rely on their homes. They saw that there was no place left and no connoisseurs either. They fled in all directions. I don’t blame them. They cannot find the material, there is no copper, aluminum, acid is expensive. The repair of the kettle costs five or six manats [about $3-3.5], and the owner thinks that for such a price it is better to buy a new one. We miss the craft atmosphere of the past.”
“I make tools out of pure steel”
The blacksmith adds that after the displacement of artisans, true masters of their craft cannot be found in the region. What distinguishes him among his colleagues is that he knows the ancient secrets of blacksmithing.
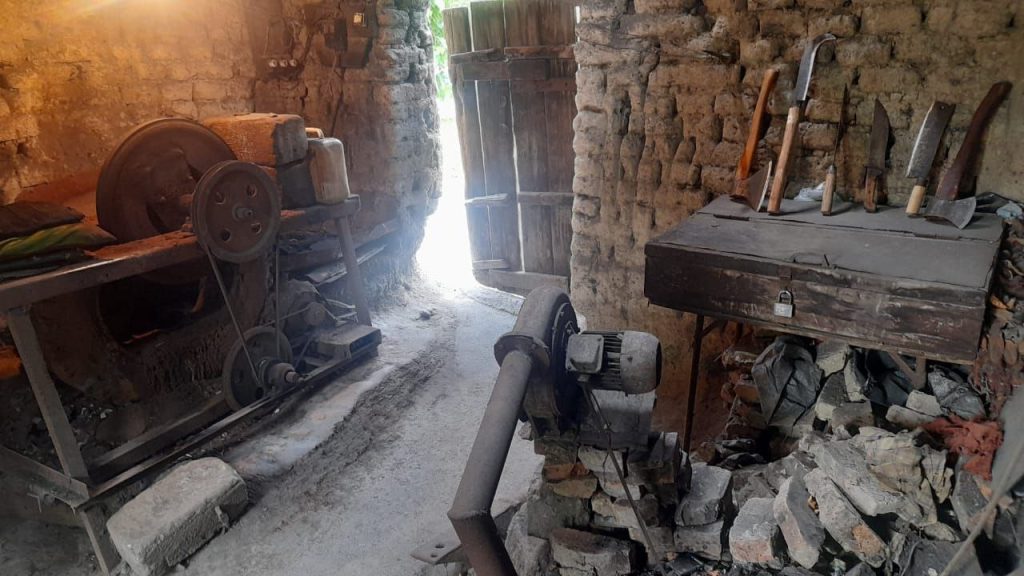
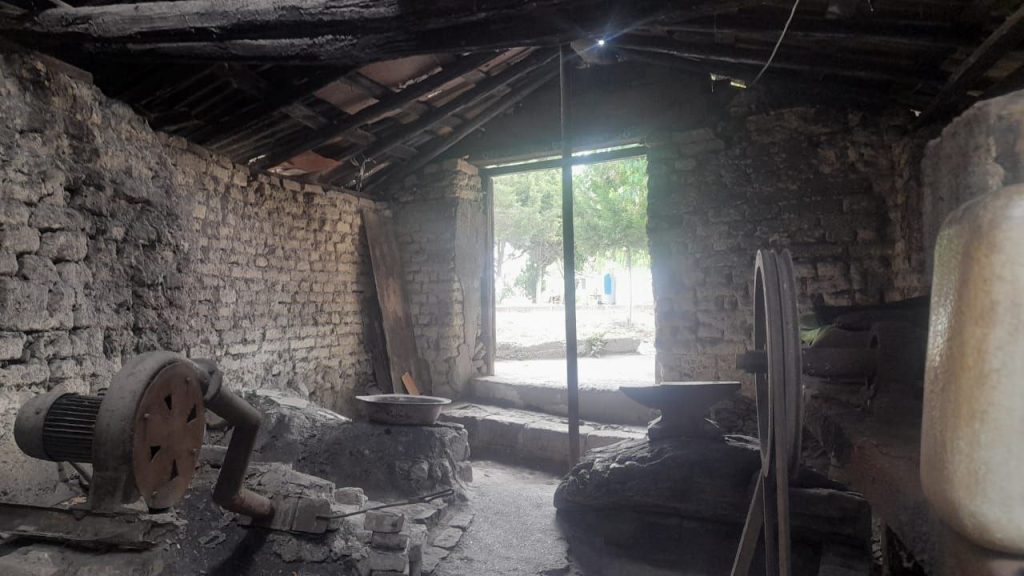
“It is impossible to build a small place, lay small stones and work as a blacksmith. I know the unique secrets of this craft, handed down to me from my ancestors, and do the work in ancient ways. I only use steel, that’s the craftsman’s choice. Others use copper to make the job cheaper. I make tools out of pure steel. The difference in quality is obvious. Iron is polished in a 25-30 manat [$15-18] sand press called tatila. They work quickly and do not splash water. It also burns the polish. There is a rule to wet the steel with water after grinding, otherwise it will not cut well. You should also wait while watering: it should turn purple so you know the iron has turned to steel. It will not work if you just put it in water and take it out. You need to use coal, not wood or charcoal.”
“Let the state support the restoration of the forge”
Now the craftsmen are worried about the problems associated with the restoration of the forge, which is considered a historical monument, and the lack of coal on the market. The promise of recovery is dragging on, coal has not been sold for several months. Expensive stone wheels are sometimes of poor quality. And all this affects the quality of the work of the master.
“There are many difficulties, but for the sake of the craft one has to make sacrifices. Most importantly, let the state support the restoration of the forge. The Ministry of Culture and Tourism arrived and conducted an inspection. The forge is registered as a historical monument, so it was not allowed to be repaired. But she’s not in good shape. In March of this year, the head of the executive power came, also examined it, and the representative of the executive power was instructed to replace the roof of the forge, restore the outer walls while maintaining their former shape. But all this remained a promise.
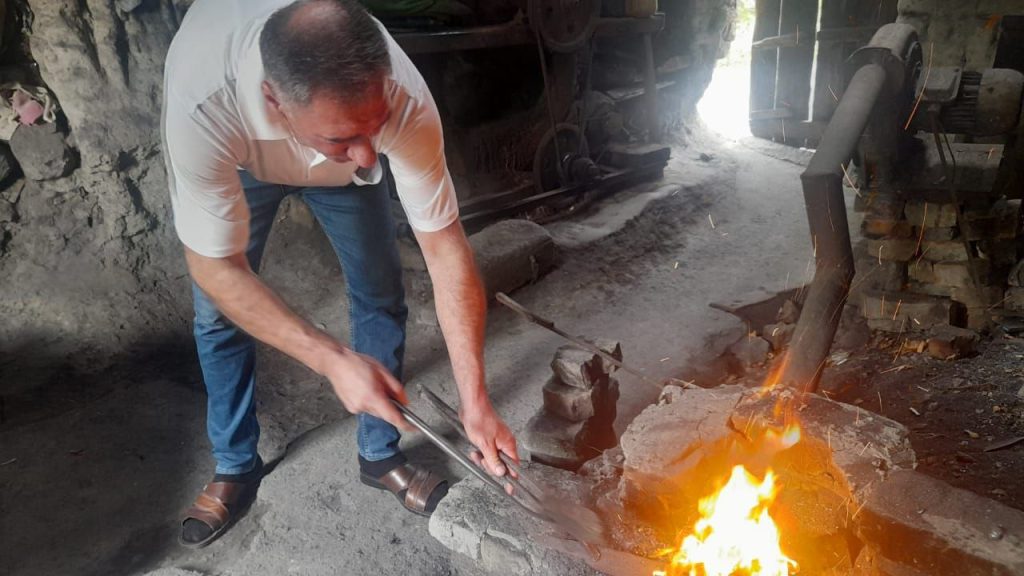
I suffer most from the lack of coal. Not found it since January. In this case, coal is very important. Charcoal does not heat up to 3000-3500 degrees. Grinding of heavy equipment is possible only in hard coal. 70 percent of my work goes through the hearth. The price of the waterwheel stone is 480 manats [about $280]. After working on the anvil, it is necessary to grind on the stone of the water wheel. And it’s hard to find in the country. Nobody uses it. The object sharpened on it does not deteriorate, does not bend, does not burn. Because waterstone is steel. We are preferred precisely because of this water stone. We brought it from Russia. But they often deteriorate, they can last a year, three years or even a month. In severe cold, they quickly break down.”
“Young people do not show patience and interest in this work”
Master Namig does not have extra income. He earns his living only by this trade. He says that today’s youth have no interest in ancient crafts. Until now, he had more than 50 students, but due to the difficulties of the work, they all left. Therefore, the master is worried about the future of ancient crafts and blacksmithing.
“This is a difficult job. Requires physical strength and interest. Today’s youth does not show patience and interest in this work. I don’t blame her, today young people don’t even have physical strength. One anvil weighs 80 kilograms. The weight of the lightest hammer is three kilograms. Sometimes I use a six-kilogram crowbar with one hand. The guys who are watching my work from the side immediately run away. Their main occupation is technology.
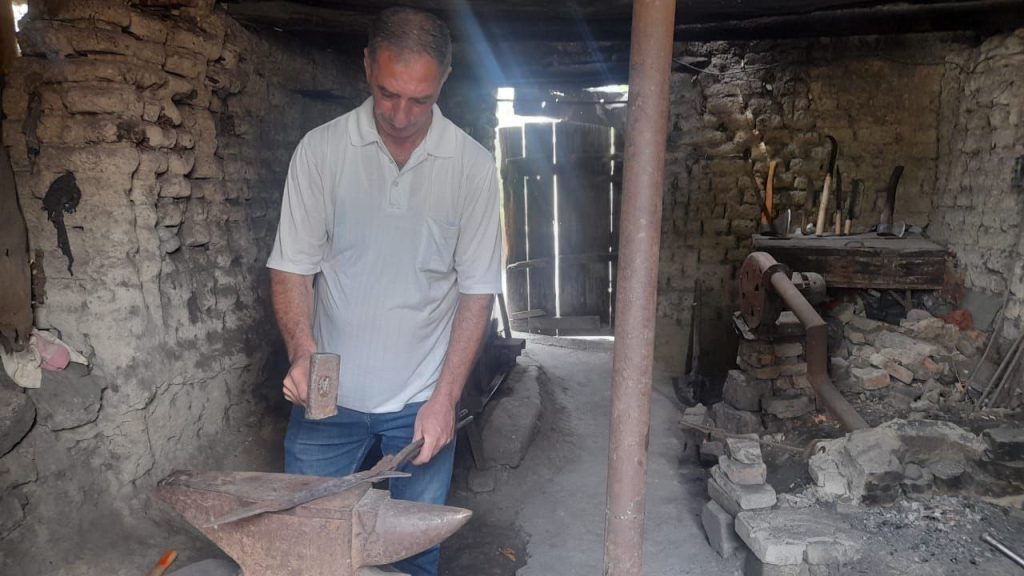
“Before, the system of work was harder, the load was greater. Customers came from different regions. The father saw that he did not have time to fulfill all the orders, called the neighbor boys and said: “Son, take these five manats [about $3] and help me.” Sometimes they worked all day without a break. They didn’t even get to eat. Later orders became much less. Now my earnings fluctuate between 50-100 manats [about $30-60] per day. But there are days when there is no income at all.”
“I wish both the craft and the forge to live”
Namig says that he came into the world as a blacksmith and will leave as a blacksmith. He intends to continue this business as long as he can. He wants only one thing, that blacksmithing and this forge, which has become a historical monument, live after it.
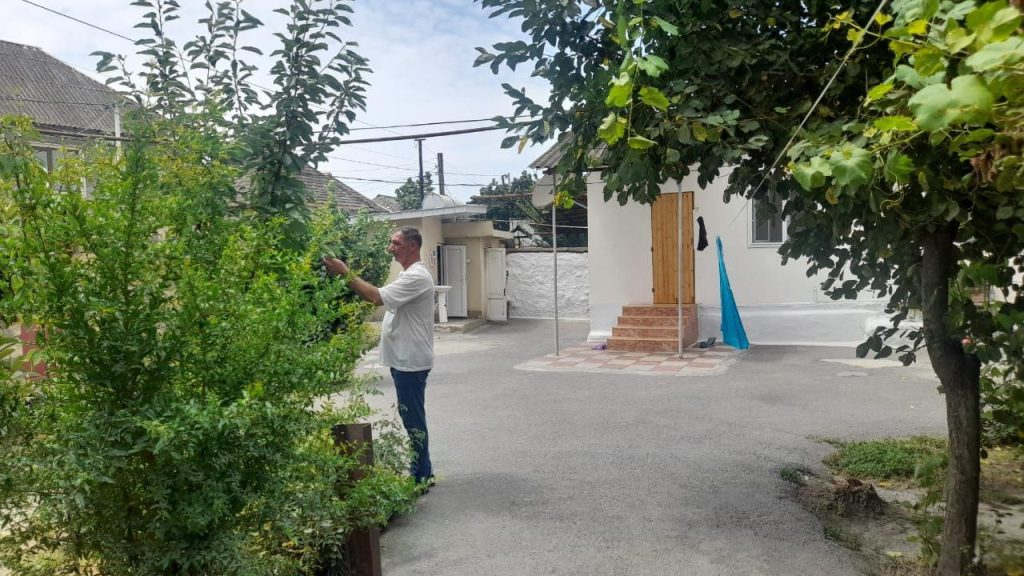
“I am proud of the art of my father and grandfather. As long as I’m alive, this craft is with me. Someone comes and places an order. I say that, they say, come in two hours, it will be ready. I finish the work exactly on time so that my word is believed. In addition to professionalism, honesty is important. Therefore, my follower must also do the same. I dream that both the craft and the forge would live.”